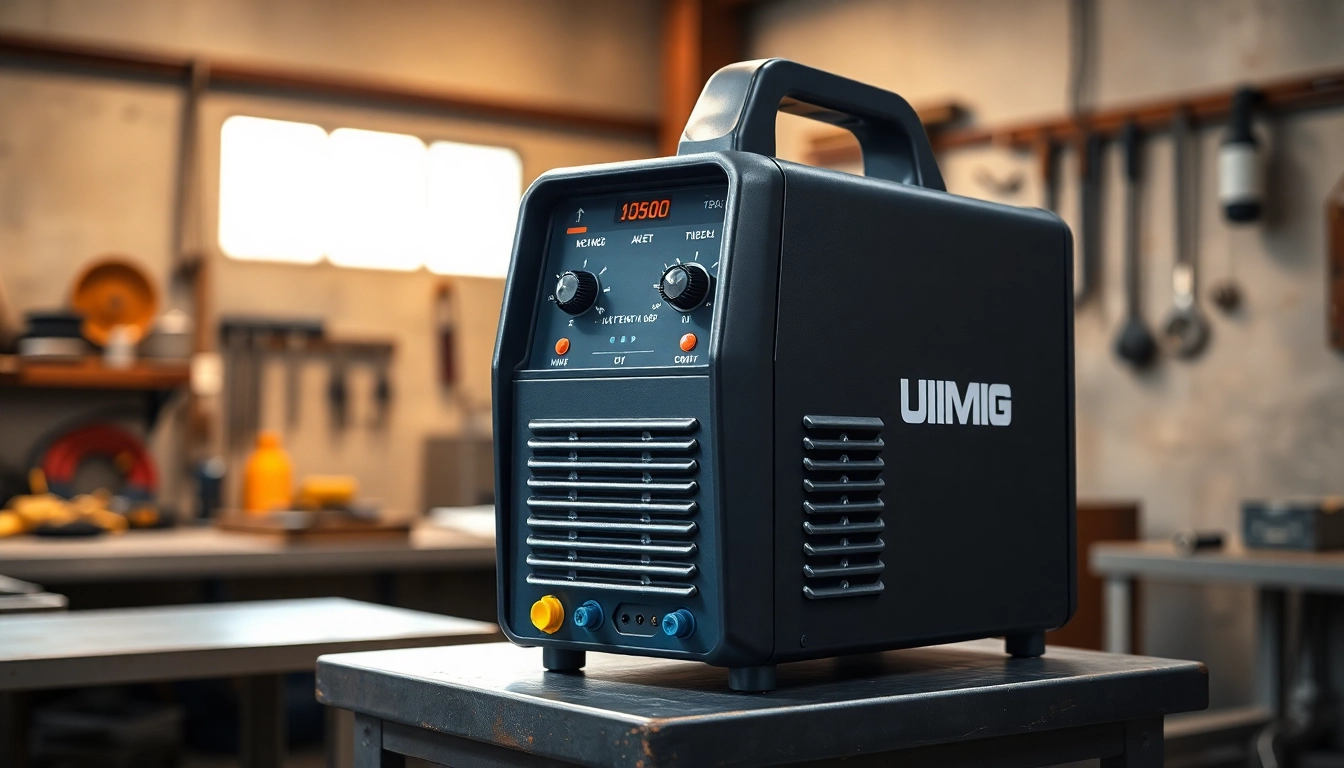
Introduction to Unimig TIG Welders
TIG (Tungsten Inert Gas) welding is a precise process that allows for high-quality welds across a variety of metals. Among the popular brands in the welding equipment market, unimig tig welder stands out for its versatility and user-friendly features. This article aims to provide an in-depth understanding of Unimig TIG welders, exploring their benefits, applications, and essential techniques for successful welding.
What is a Unimig TIG Welder?
A Unimig TIG welder utilizes an inert gas to shield the weld area from atmospheric contamination, ensuring clean, strong welds. These machines come equipped with features that cater to both novice welders and seasoned professionals, making them suitable for an array of welding tasks. Unimig TIG welders are notable for their efficiency and reliability, often preferred in various industries due to their ability to weld thin materials and produce aesthetically pleasing results.
Benefits of Using Unimig TIG Welders
Unimig TIG welders offer numerous benefits, tailored to meet user demands. Key advantages include:
- High Precision: The arc control and pedal options enable precise adjustments, crucial for thin materials.
- Versatility: Capable of welding different types of metals, including aluminum, stainless steel, and magnesium.
- Cleaner Welds: The inert gas shielding helps produce less spatter and a smoother finish.
- Adjustable Settings: Welders can easily adjust voltage and amperage settings, giving them control over the weld characteristics.
- User-Friendly: Many models incorporate intuitive controls and features that simplify the learning curve for beginners.
Common Applications in Different Industries
Unimig TIG welders are utilized in various industries, reflecting their capability and adaptability. Common applications include:
- Aerospace: Due to the stringent requirements for quality and strength in components.
- Automotive: For repairing and customizing vehicles with high aesthetic and structural standards.
- Manufacturing: Used in the production of small parts where precision is crucial.
- Art and Sculpture: Artists leverage TIG welding for creating intricate works from metal.
- Pipe and Tube Welding: Ideal for creating strong joints in plumbing and HVAC systems.
Understanding TIG Welding Basics
Key Components of a TIG Welder
Understanding the components of a TIG welder is essential for effective use:
- Tungsten Electrode: The non-consumable electrode responsible for creating the arc.
- Welding Torch: Directs the flow of shielding gas and molten filler metal.
- Gas Supply: Typically argon, providing an inert atmosphere.
- Power Source: Supplies the required electricity to the electrode and controls the welding current.
- Cooling System: Essential for managing the heat generated during welding.
How TIG Welding Works
TIG welding involves several steps for successful execution:
- Setup: Prepare the work area, ensuring proper ventilation and cleanliness.
- Powering On: Start the welder and set desired parameters based on material type and thickness.
- Creating an Arc: The tungsten electrode creates an arc when brought near the metal surface.
- Filler Material Addition: As the base metal melts, the welder can manually feed filler material into the molten pool.
- Controlling the Speed: The welder controls the torch movement and filler rod feed rate to maintain the desired weld appearance.
Safety Precautions for TIG Welding
Safety is paramount in any welding process. Key safety precautions include:
- Wearing protective gear: gloves, welding helmets with appropriate shade, and long-sleeved clothing.
- Ensuring proper ventilation to avoid inhaling harmful fumes.
- Regularly inspecting the equipment for wear or damage.
- Staying alert and cautious of surroundings to prevent accidents.
Choosing the Right Unimig TIG Welder
Comparison of Popular Models
Unimig offers several models suited for various needs. Comparing them based on power, features, and intended applications can help in selecting the right model:
- Unimig Razor 200 AC/DC: Known for its versatility, this model is ideal for both aluminum and stainless steel.
- Unimig Viper 180 AC/DC Mk II: Designed for beginners, it comes with user-friendly features and a lightweight design.
- Unimig VIPER MULTI 195 MAX: Offers advanced features like integrated digital display, making it suitable for professionals seeking precision.
Factors to Consider When Purchasing
When selecting a TIG welder, consider the following:
- Power Requirements: Ensure the welder’s amperage is suitable for the thickness and type of material.
- Portability: Check if the welder needs to be moved frequently; options with wheels or lighter designs may be preferable.
- Features: Look for features such as TIG torch flexibility, digital displays, and foot pedal control.
- Warranties and Support: Choose a brand that offers reliable customer support and warranty options.
Pricing and Budgeting
The cost of Unimig TIG welders varies based on features and specifications. Basic models can start from around $1,200, while advanced units can exceed $2,000. Budgeting should account for additional costs such as:
- Consumables: electrodes, filler materials, and shielding gases.
- Protective gear and safety equipment.
- Maintenance and repair services.
Techniques for Effective TIG Welding
Setting Up Your Unimig TIG Welder
Setting up the welder correctly is crucial for achieving quality welds. Steps include:
- Install the tungsten electrode in the welding torch, ensuring it’s secured properly.
- Attach the work lead to the base metal being welded.
- Set up the gas supply, ensuring proper flow and tight connections.
- Adjust the welder settings according to the thickness and type of metal.
Common Welding Techniques and Tips
Mastering techniques is critical for successful welding. Here are several tips to consider:
- Maintain a consistent travel speed to avoid uneven welds.
- Keep an appropriate distance between the tungsten and the workpiece.
- Practice controlling the heat input, especially for thin materials.
- Use a filler rod that matches the base metals for stronger welds.
Troubleshooting Common Issues
Even experienced welders encounter issues. Here are common problems and their solutions:
- Undercuts: Often caused by too much heat; reduce the amperage or adjust travel speed.
- Porosity: Indicates contamination; ensure cleanliness of the work area and use proper gas coverage.
- Inconsistent Arc: Check for obstructions in the torch or improper setup of the gas supply.
Maintaining Your Unimig TIG Welder
Regular Maintenance Practices
Maintaining your Unimig TIG welder is key to longevity and performance. Regular tasks include:
- Inspecting and cleaning the torch and welding contacts.
- Replacing worn consumables such as tungsten electrodes and LLC.
- Checking the gas lines for leaks and regularly replacing the shielding gas.
Identifying When to Seek Professional Help
While many maintenance tasks can be performed by users, certain issues may require professional servicing:
- Severe electrical issues or sparks around the power source.
- Inconsistent or weak arc performance that cannot be fixed with standard adjustments.
- Physical damage to the welder that affects its integrity or safety.
Extending the Lifecycle of Your Welder
To ensure your Unimig TIG welder remains in optimal condition, consider the following:
- Follow manufacturer recommendations for use and maintenance.
- Avoid overloading the welder beyond its rated capacity.
- Store the welder in a clean, dry area to prevent rust and damage.
- Regularly update your knowledge about new techniques and practices in TIG welding.
Conclusion
Mastering the use of a Unimig TIG welder can significantly enhance your welding capabilities, whether you’re in a professional setting or working on personal projects. By understanding the mechanics of the machine, applying effective techniques, and adhering to maintenance best practices, you can achieve high-quality welds consistently. The versatility, efficiency, and reliability of Unimig TIG welders place them as a vital component in any welding toolkit.