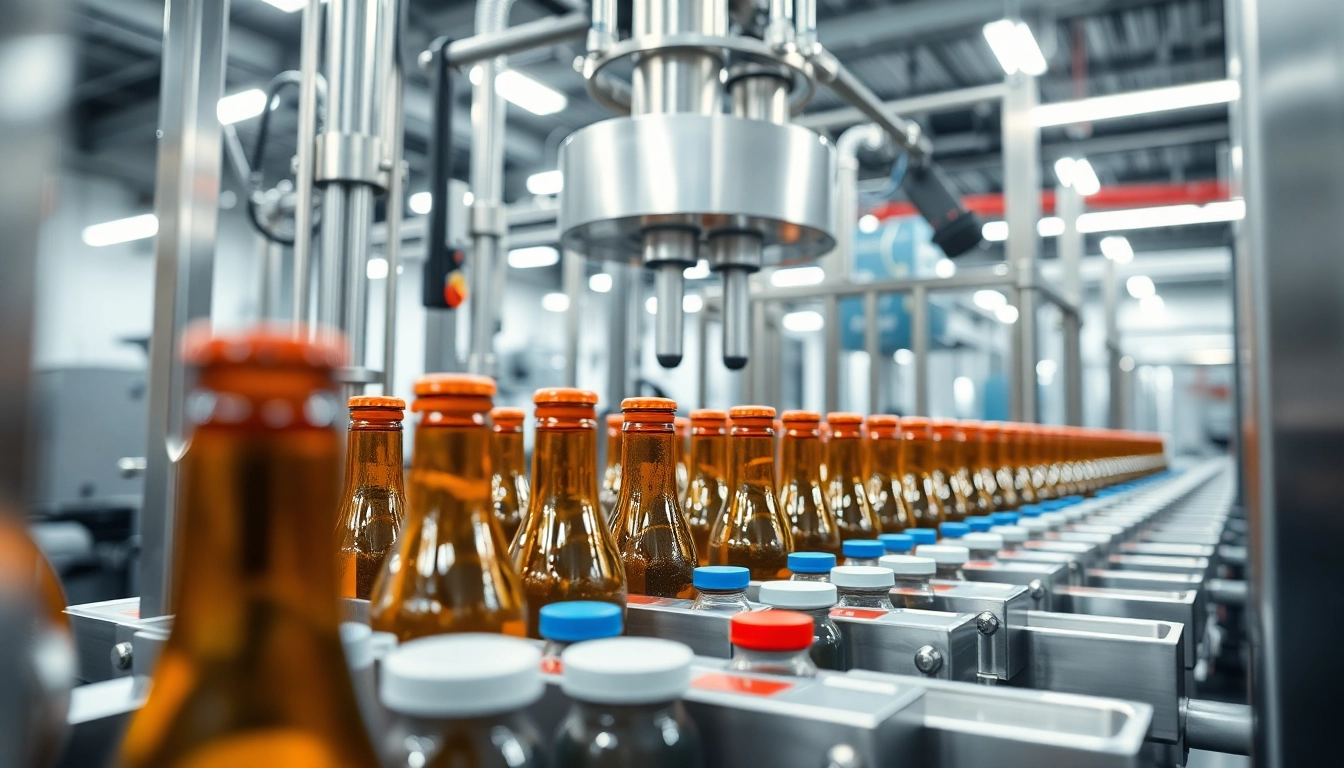
Understanding Filling Machines
What are Filling Machines?
Filling machines are essential industrial equipment used to dispense a precise volume of a product into containers. These machines are prevalent in various sectors, including food and beverage, pharmaceuticals, cosmetics, and chemicals. Their primary function is to automate the bottling or packaging process, ensuring consistent product quantities, reducing manual labor, and enhancing production efficiency. In many cases, these machines are equipped with advanced technology that allows for the filling of a wide range of liquids, from water and oils to creams and pharmaceuticals.
Types of Filling Machines Available
Filling machines come in different types and configurations, each suited for specific applications. Here are some of the most common kinds:
- Piston Filling Machines: Ideal for thick liquids, paste, and semi-solid products, these machines use a piston to draw in the product and then discharge it into the container.
- Gravity Filling Machines: Utilizing gravity to fill bottles, these machines are best suited for thin liquids like water and juice.
- Vacuum Filling Machines: These machines remove air from the bottle before filling, ensuring that the product is packed tightly and retains freshness.
- Pump Filling Machines: Equipped with an adjustable pump, these machines can handle a variety of liquid viscosities, making them highly versatile.
- Overflow Filling Machines: Used when precise filling is required, these machines fill containers to a specific level, ensuring consistency across all units.
The Importance of Choosing the Right Supplier
When it comes to investing in filling machines, partnering with a reliable Filling Machine Supplier is crucial. A good supplier not only provides quality equipment but also understands the specific needs of different industries. They ensure that the machinery complies with industry standards, is fitted with the latest technology for optimal performance, and comes with robust after-sales support. Selecting a supplier with extensive experience can significantly influence the efficiency and productivity of your operations.
Key Features of Quality Filling Machines
Accuracy and Precision in Filling
Precision is paramount in filling operations. High-quality filling machines are designed to deliver accurate fill levels, which is crucial for avoiding overfills or underfills that can lead to product wastage and customer dissatisfaction. Systems equipped with advanced sensors and programmable logic controllers (PLCs) ensure that every bottle is filled consistently, enhancing overall product quality and regulatory compliance.
Adaptability for Various Liquids
Not all filling machines can handle the diverse array of products available on the market. A quality filling machine should be adaptable, capable of handling various types of liquids, including viscous substances, foamy liquids, or those requiring controlled temperatures. This adaptability enables a single filling machine to be used across multiple production lines, reducing capital expenditure and increasing flexibility.
Efficiency and Speed in Production
Operational efficiency is a critical factor in any production process. High-speed filling machines can significantly reduce downtime and maximize output. The best filling machines are capable of automated processes that require minimal human intervention, thus speeding up the entire production line while maintaining high-quality standards. Features such as quick changeover capabilities for different bottle sizes and products further enhance efficiency.
Top Considerations When Selecting a Filling Machine Supplier
Reputation and Industry Experience
The reputation of a filling machine supplier speaks volumes about the reliability and quality of their products. Research potential suppliers to understand their standing in the industry. Look for reviews, testimonials, and case studies that highlight their expertise and customer satisfaction. A supplier with years of experience typically understands market trends and can offer machines that meet current demands and future advancements.
Customer Support and Services Offered
Robust customer support is integral to maintaining production efficiency. Consider suppliers who offer extensive training, installation services, and a reliable maintenance contract. A supplier who stands by their product with excellent post-sales support can save businesses time and money in the long run.
Technological Innovations and Options
The landscape of filling technology is ever-evolving. It’s essential to choose a supplier that invests in state-of-the-art innovations, offering machines that are not just compliant with current standards but are also future-ready. This includes options for automation, connectivity, and integration with other automated systems, such as capping and labeling machines, to create a fully seamless production line.
Common Applications of Filling Machines
Food and Beverage Industry
The food and beverage industry is one of the largest consumers of filling machines. These machines are used to fill products such as sauces, juices, dairy products, and alcoholic beverages. The importance of hygiene and compliance with food safety regulations cannot be overstated; thus, filling machines must meet stringent health standards to ensure product safety and quality.
Pharmaceutical Sector
In the pharmaceutical industry, precision in filling is crucial. Filling machines must be designed to handle sterile environments and comply with specific regulatory requirements. They are typically used for packaging medicines, vaccines, and health supplements in varying forms such as liquid drops, syrups, and powders. The ability to adapt to different vial sizes and shapes plays a significant role in ensuring that production lines remain flexible and efficient.
Cosmetic and Chemical Industries
Cosmetic products often come in diverse forms, from creams and lotions to liquids and gels. Filling machines in this sector are designed for high versatility to accommodate the varying viscosities of products. Similarly, the chemical industry relies on automated filling processes to ensure accuracy when packaging household cleaners, lubricants, and other chemical products to mitigate risks and improve efficiency.
Maximizing Efficiency with Your Filling Machine
Regular Maintenance and Upkeep
Regular maintenance extends the lifespan of your filling machine and prevents costly downtime. Establishing a structured maintenance plan that includes routine checks, cleaning, and timely replacement of worn parts can significantly improve the machine’s efficiency. Consistent performance monitoring allows for the identification of potential issues before they lead to equipment failures.
Staff Training and Best Practices
Your staff is the backbone of your production line. Providing comprehensive training on how to operate the filling machine correctly maximizes its efficiency and minimizes error rates. Training should cover machine operation, troubleshooting minor issues, and understanding how to maintain consistent quality standards. Encouraging best practices among staff can lead to significant improvements in overall production output.
Measuring Performance and Success Rates
To assess the effectiveness of your filling machine, it’s crucial to establish key performance indicators (KPIs). Metrics such as filling accuracy, speed, downtime, and operational efficiency can help pinpoint areas for improvement. Conducting regular audits can provide further insights into the machine’s performance and highlight trends that may require attention.