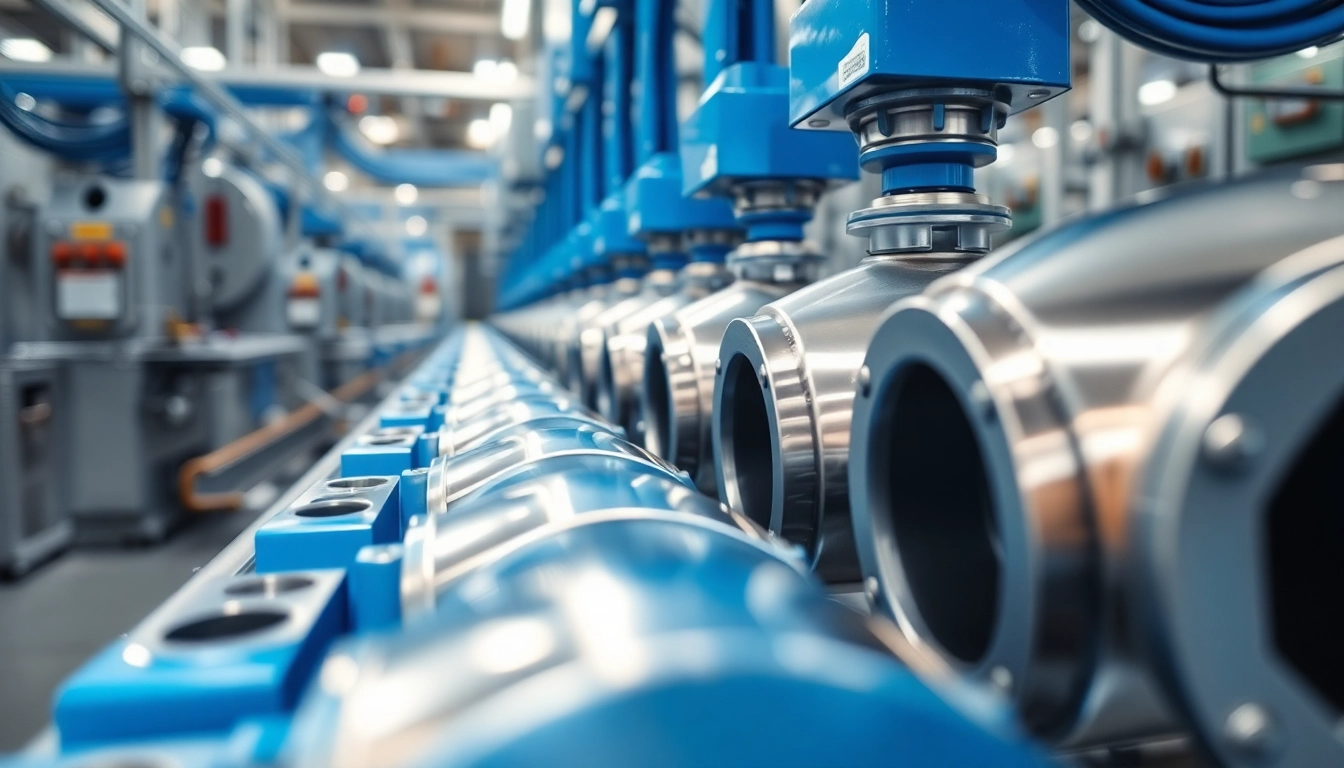
What is EP Coating?
Definition and Importance of Electrophoretic Coating
Electrophoretic coating, commonly referred to as ep coating, is an advanced finishing technology utilized predominantly for metal components. The process involves the use of an electric current to deposit coating materials, mainly paints, onto conductive surfaces. This method is vital in sectors such as automotive, industrial machinery, and household appliances, due to its robust ability to provide superior corrosion resistance and durability.
EP coating functions not only as a protective layer but also serves an aesthetic purpose, enhancing the visual appeal of products. The significant advantage lies in its uniformity—electrophoretic coating ensures a consistent finish even in complex geometries, which are often challenging for traditional painting methods. In essence, EP coating is a crucial part of modern manufacturing, marrying operational efficiency with premium performance outcomes.
How EP Coating Works: The Science Behind it
The electrophoretic coating process involves moving charged paint particles toward a substrate, which is oppositely charged. The particles are dispersed in a water-based solution, and when an electric field is applied, they migrate towards the surface of the substrate, adhering and forming a continuous film.
This process is comprised of several key steps:
- Preparation: Substrates must be thoroughly cleaned and treated to ensure optimal coating adhesion. This may involve processes like phosphating, which enhances corrosion resistance.
- Electrophoretic Deposition: Once the parts are submerged in the coating bath, the electrical current is turned on, prompting charged particles to deposit onto the surface.
- Curing: After deposition, the coated parts are cured using heat to facilitate cross-linking within the coating, enhancing its mechanical strength and durability.
This sophisticated interplay of electrostatics and chemistry allows for an even and resilient coating that can withstand harsh environmental conditions.
Common Applications in Various Industries
EP coating finds extensive applications across a variety of industries. Here are some of the most common:
- Automotive Industry: EP coating is widely used in automotive manufacturing for parts such as body panels, chassis, and engine components to ensure long-lasting protection against corrosion and wear.
- Electronics: In the electronics sector, EP coatings protect sensitive components from environmental factors like moisture and dust, prolonging their operational life.
- Aerospace: The lightweight, durable coatings enhance the performance of aerospace components, ensuring they meet rigorous safety and performance standards.
- Household Appliances: Many appliances use EP coatings to provide aesthetic appeal while safeguarding against degradation and wear from usage.
Benefits of EP Coating
Enhanced Corrosion Resistance for Metal Components
One of the primary benefits of EP coating is its superior corrosion resistance. The electrochemical characteristics of the coating provide a robust barrier against environmental elements such as moisture, salts, and pollutants that typically contribute to corrosion. This protective layering is especially beneficial in industries where equipment is constantly exposed to harsh conditions.
Industry data shows that EP-coated materials have up to five times longer lifespans compared to uncoated counterparts in corrosive environments, reducing maintenance costs and downtime significantly.
Cost-Effectiveness Compared to Other Coatings
When it comes to cost efficiency, EP coating offers remarkable advantages. Although initial investment in the equipment and setup may be higher compared to some traditional coating methods, the longevity and durability of the coating can lead to significant savings over time. Additionally, the reduced need for touch-ups and reapplication further enhances its cost-effectiveness. Companies can save on both labor and materials, making it a financially smarter choice in the long run.
Environmentally Friendly Aspects of EP Coating
As industries increasingly aim for sustainability, EP coating comes out as a champion. The process uses water-based solutions which emit fewer volatile organic compounds (VOCs) compared to solvent-based coatings, resulting in a lesser environmental impact. Moreover, the efficient application of coatings reduces waste and ensures that more of the material ends up on the product rather than in the environment.
These environmentally conscious aspects make EP coating an attractive option for companies looking to comply with stricter environmental regulations and guidelines without sacrificing performance.
EP Coating Process Overview
Step-by-Step Guide to the Electrophoretic Coating Process
The EP coating process can be broken down into distinct steps:
- Cleaning: Parts are cleaned with detergents or solvents to remove all contaminants.
- Surface Preparation: Techniques such as sandblasting or phosphating are employed to enhance substrate adhesion.
- Bath Preparation: Coating materials are mixed in a water-soluble form and the bath is prepared to the required conductivity levels.
- Electrophoretic Deposition: The substrate is submerged into the coating bath, and a voltage is applied to initiate particle movement. The time duration varies based on desired coat thickness.
- Rinsing: Excess coating is removed from the surface with water rinse.
- Curing: Coated items are cured, often at elevated temperatures, to harden the coating and enhance adhesion.
Types of Coating Materials Used
Multiple types of resins and polymers can serve as the medium in EP coating processes. These materials are selected based on desired characteristics. Common types include:
- Acrylics: Known for their clarity and gloss, often used where appearance is critical.
- Polyesters: Provide excellent mechanical properties and chemical resistance, suitable for automotive applications.
- Vinyls: Offer good flexibility and adhesion properties, commonly used in consumer products.
The choice of materials fundamentally affects the performance and quality of the final coating, and thus consideration is paramount during the planning phase.
Quality Control Measures in EP Coating
Ensuring high quality through every step of the EP coating process is crucial. Industries implement rigorous quality control measures such as:
- Visual Inspection: Regularly checking for defects or inconsistencies in coating.
- Thickness Measurements: Employing non-destructive testing methods to ensure the coating thickness meets specifications.
- Chemical Resistance Testing: Subjects coated items to simulated environmental conditions to assess durability.
- Cross Hatch Adhesion Tests: Measures how well the coating adheres to the substrate, ensuring longevity.
These practices help maintain production standards and build consumer confidence in coated products.
EP Coating vs. Other Coating Methods
Comparing EP Coating to Powder Coating
EP coating and powder coating are two of the most prevalent methods in the market, and while they serve similar purposes, they have distinct differences:
- Application Process: EP coating uses an electric charge to attract paint particles while powder coating relies on electrostatic charge but is applied in dry powder form.
- Curing: EP coatings usually require a heat cure to finish, whereas powder coatings cure through heat once applied.
- Thickness: EP coatings are often thinner and provide a smoother finish compared to powder coatings, which can be thicker but more textured.
Choosing between these methods depends largely on specific project requirements, including desired aesthetics, mechanical properties, and environmental conditions.
Advantages of Electrophoretic Coating over Traditional Coatings
Electrophoretic coating stands out due to its several advantages over traditional coating methods such as spray painting and dip coating:
- Uniformity: EP coatings provide even coverage, reaching complex shapes and recesses where traditional methods may fail.
- Efficiency: The controlled deposition allows for less waste and reduced overspray compared to spray painting.
- Improved Adhesion: The bonding chemical properties foster superior adhesion levels on various substrates.
The technological efficacy of EP coating makes it a favorable choice across diverse applications in modern manufacturing.
Which Method is Best for Your Project?
When deciding on a coating method, consider the project’s specific requirements such as:
- Material characteristics – What substrate are you coating?
- Environmental exposure – What kind of conditions will the coated item face?
- Aesthetics – Is the visual appearance of the coating a priority?
- Cost and durability – What are the budgets and expected lifespans of the components?
Analyzing these factors will guide manufacturers in selecting the most suitable coating method for optimal performance and cost-efficiency.
Future Trends in EP Coating Technology
Innovations in Coating Materials and Processes
The future of EP coating is marked by continual innovation. Advancements such as nanotechnology are paving the way for new materials that enhance coating properties while further minimizing environmental impacts. These innovations promise to increase thermal resistance and further improve durability, allowing coated products to meet even more demanding applications.
The Impact of Industry 4.0 on EP Coating
As manufacturing moves toward Industry 4.0, EP coating technology is expected to integrate smart technologies that allow for real-time monitoring and adjustments throughout the coating process. Automation, data analytics, and improved monitoring systems are expected to create personalized coatings, optimized formulations, and enhanced quality control. These developments will further streamline processes and improve overall production efficiency, thus reducing costs and waste.
Predictions for the Future of Electrophoretic Coating
Looking ahead, the electrophoretic coating process is likely to become a standard in many additional industries, necessitated by the rising focus on sustainability and durability in product manufacturing. As consumers demand longer-lasting products, industries may see a rapid transition to EP coating as a reliable solution. Furthermore, the push for eco-friendly materials will also enhance the push towards more extensive use of water-based formulations in the coming years.